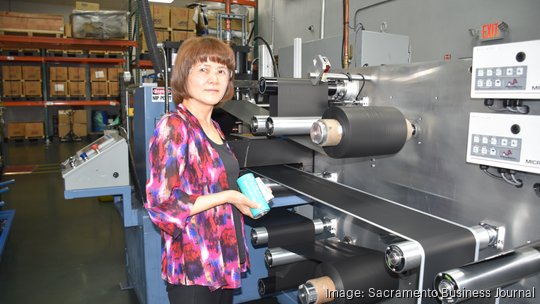
The California Energy Commission will consider a $2.9 million grant to fund a pilot production line for battery cathodes developed by LiCAP Technologies Inc. in Rancho Cordova.
LiCAP's project is on the commission's agenda for its June 16 meeting in Sacramento.
The company has been making battery cathodes on a custom basis. The grant money could help fund an automated faster line, said LiCAP President Linda Zhong.
LiCAP has already built a production line for capacitor cathodes, which it has been selling for years.
The new line is for battery cathodes using LiCAP's patented dry manufacturing process.
The energy commission grant is from its Electric Program Investment Charge, or EPIC, program that provides money for scientific research to transform electric technology to meet the state's energy and climate goals.
The commission in its agenda says LiCAP's "patented electrode production process offers significant advantages over the traditional 'wet coating' process including lower energy consumption, reduced amount of CO2 emissions, lower manufacturing footprint, improved battery performance, and elimination of toxic solvents from electrode manufacturing."
Separately, LiCAP is trying to raise $40 million in the next few months to further expand its capacity to produce electrodes for lithium batteries using its patented dry technology. It's getting about $10 million from Japanese and German original equipment manufacturers, who Zhong has declined to name. LiCAP is raising the other $30 million from investors.
The OEMs are very interested, Zhong said. "We have lots of interest. Our customers are constantly asking for more material."
Zhong has been granted 97 patents and she has 19 pending, many for electrode and capacitor products and techniques.
The electrode is a major battery component. For most existing batteries, a wet process is used to make electrodes.
The dry manufacturing process developed by LiCAP doesn’t produce toxic materials and uses less energy than the current standard process. LiCAP’s electrode manufacturing process also takes minutes rather than hours, and it avoids the use of solvents that are dangerous to workers and potentially explosive.
To make LiCAP's ultracapacitors, the company's 40 local employees use custom-built equipment to process activated carbon powder into a substance with the consistency of cotton candy. It then rolls out that material into thin sheets of carbon. After the first rollout, the material looks like rolls of black paper. The process then laminates two sheets with an aluminum anode bonded at the ends. That material, wound tightly into a canister, is the business end of a capacitor or a battery.