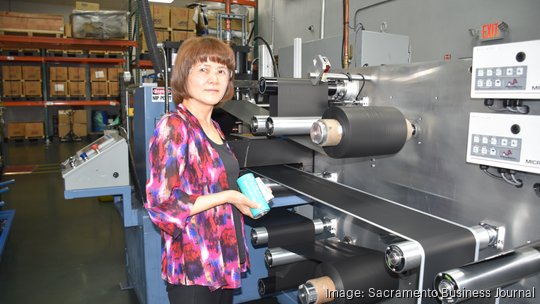
LiCAP Technologies Inc. is planning to raise $40 million to scale up its manufacturing of battery technology in Rancho Cordova.
LiCAP has developed a process that uses less power and avoids the use of toxic materials compared with the current standard wet-coating process to make electrodes for lithium-ion batteries, capacitors and ultracapacitors.
Founder and CEO Linda Zhong said the company is raising $40 million in the next few months to expand its manufacturing to produce lithium batteries using its patented dry electrode technology.
She said the company is getting about $10 million from original equipment manufacturers, whom she declined to identify, and is raising $30 million from investors.
LiCAP has 40 full-time employees in Rancho Cordova, and it works with a sister company that does assembly in China.
LiCAP's assembly line in Rancho Cordova now makes carbon electrodes for ultracapacitors, and the company is completing a new line for lithium-ion electrodes for batteries.
Batteries have applications for the electric grid and future transportation. Ultracapacitors have applications to work onboard electric vehicles to absorb repeated fast spikes of generated electricity, such as in regenerative braking, and fast discharges such as acceleration.
One of the first high-profile applications for LiCAP's early ultracapacitors was in wind turbines. Unstable wind conditions require wind turbines to be able to adjust the pitch of their blades to compensate for turbulence or to not spin too quickly, Zhong said. The industry used onboard batteries to power those rotation motors, but the batteries needed to be replaced every couple of years because rapid cycling wears them out, and it is a dangerous chore to replace them. That is a perfect application for ultracapacitors, which can last 20 years, Zhong said.
LiCAP's patented technology mostly changes the manufacturing process for cathodes from what the industry uses now, which is a wet solvent-based approach followed by a drying period where solvents must be evaporated and recovered, which takes energy and time.
The manufacture of electrodes using LiCAP’s Activated Dry Electrode method uses about 70% less energy than the wet process. It's also faster, and excess material can be recycled on site.
LiCAP's dry electrode production line is about 30 feet long. A wet electrode line would go have to be 10 times larger, said Martin Zea, LiCAP's director of operations.
Some of LiCAP’s manufacturing advantages come from lower energy consumption in the manufacture of battery components, giving batteries that use its technology a lower carbon footprint.
LiCAP was the overall winner in 2022 for the Innovation of the Year in the Business Journal's Sacramento Region Innovation Awards, picked by a panel of local innovation leaders and Business Journal staff.