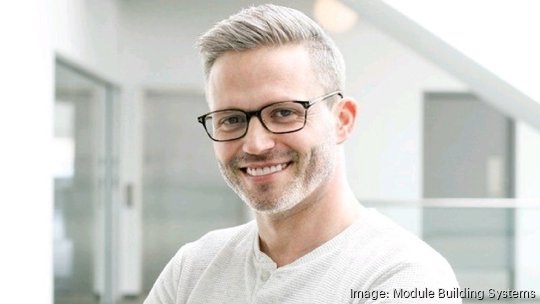
Mark Turnbull sais he knew he’d one day be relocating from his home country of Canada after launching construction technology company Module Building Systems (MBS).
While Turnbull said it’s something Canadians wouldn’t like to hear, he claims Canada is “just not open for business” for a company like his due to its building code requirements.
“Introducing a new building technology like ours requires you to go through leaps and hurdles with the Canadian government,” Turnbull said.
Turnbull is founder and CEO of MBS, which launched in 2019. The firm has created a construction system it says can make building panels off-site, providing “ready-to-assemble” buildings that can be developed more quickly than with traditional construction methods. Turnbull said he believes the company’s technology could be used in commercial real estate projects, while also being an option to use for affordable housing and disaster relief.
Turnbull targeted the U.S. as MBS' home base soon after launching the company, considering several cities for its headquarters. In addition to St. Louis, options included Los Angeles; Memphis; Nashville, Tennessee; Las Vegas; and Everett, Washington.
“Everything just kind of clicked in St. Louis. It just made sense,” Turnbull said. “You're landlocked in the middle of America. You have the Mississippi for shipping our panels on barges. You have an incredible infrastructure system of rail and road, highways and whatnot.”
Turnball made his first trip to St. Louis in December 2022. That visit prompted his decision to relocate here, where he has ingrained himself in the community. He’s added several St. Louisans, including Build-A-Bear Workshop founder Maxine Clark, to his firm’s advisory board. Turnbull said MBS has entered into a workforce training partnership with Ranken Technical College and has a letter of intent with Good Developments Group, the entity behind the proposed $1.2 billion Gateway South construction innovation district planned just south of the Gateway Arch.
“The collaboration centers on the multiyear Gateway South project at Chouteau's Landing, where MBS will play a pivotal role in implementing our panelized building system. The partnership is poised to achieve significant cost savings and efficiency by utilizing MBS' cutting-edge technology,” Turnbull said.
He said the connection system used for MBS’ building panels is its “secret sauce.” MBS’ panels, made off-site, include metal rods that are tightened into the floor sections of a building, Turnball said. The foundation of a building developed with MBS’ technology includes a “rail system” that puts the panels in place. Turnbull likens the system to putting together ready-to-assemble furniture that requires using screws and nuts to tighten pieces and hold them in place.
MBS has yet to commercialize its construction system, with Turnbull saying that will occur once it has a manufacturing facility. It plans to move into a 30,000-square-foot space inside the former Killark Electric headquarters at 3940 Martin Luther King Drive, according to Turnbull. The Land Clearance for Redevelopment Authority, the city’s urban renewal board, in October 2023 acquired the 150,000-square-foot building to use as a workforce development hub. Turnbull said MBS will temporarily be based at Ranken Technical College’s campus prior to relocating to its permanent space.
MBS positions its technology as a faster and more affordable way to do construction. Turnbull said a 5,000-square-foot project could be manufactured in two weeks, assembled in three days, with the finishings on the building taking a week or two to finish. He estimates its construction system is about 30% cheaper than traditional building methods.
“We overlap site work and foundation work time with the manufacturing of the actual superstructure itself. That expedites the time line roughly around 50% compared to traditional construction,” Turnbull said.
MBS envisions working on commercial projects and providing its technology to be used for temporary housing after natural disasters. Turnbull described himself as a “humanitarian at heart,” saying he’s visited Haiti 15 times. The company also wants to work with nonprofits on creating affordable housing, he said. The company’s technology can be disassembled, allowing it to be reused at different disaster sites, according to Turnbull.
“We could actually refurbish our panels, relocate the buildings and create an ecosystem of recyclable or renewable [buildings],” he said.
Turnbull said he has personally invested about $100,000 to $150,000 to operate MBS. The company is currently seeking to raise $4 million in capital in a pair of $2 million tranches. The initial $2 million would be part of a $10 million New Market Tax Credits package, he said. The additional $2 million would be used to aid operations. MBS in November 2023 won a $75,000 grant from St. Louis nonprofit Arch Grants, which gives equity-free funding to startups.
Turnbull has a background in web developing, and said he taught himself web coding and later started a media firm. That led to a background in real estate development, where he said he learned more about construction. Turnbull said his decision to relocate to St. Louis has been a long time coming.
“My dream since I was a little kid was to work and live in the United States. I was fortunate. When I was young, I went on a family motorhome trip when I was 11, and I saw just how beautiful the country is,” he said.