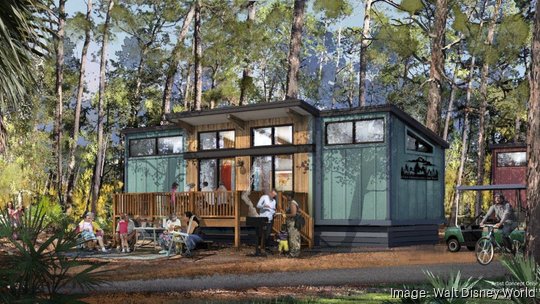
The ultimate Disney souvenir is now available on Facebook for $49,900. This is not a joke. If you’re in the market for a used tiny home of about 500 square feet that until now has lived on Disney's Fort Wilderness Resort & Campground grounds, you can have it.
Exposed ceiling beams are a design highlight and delivery is available within 25 miles of Orlando. An undisclosed number are available; the deal is good until they’re gone.
They are being replaced rapidly by new cabins that still have the rustic Fort Wilderness finishes — but less environmental impact and more creature comforts, like a basin cabinet and full kitchen. In fact, the goal is to build 365 of the new cabins in 365 days.
Fort Wilderness has migrated into the Disney Vacation Club portfolio, which is what kicked off the development of new accommodations, said Todd Watzel, senior manager of facilities asset management at Walt Disney World.
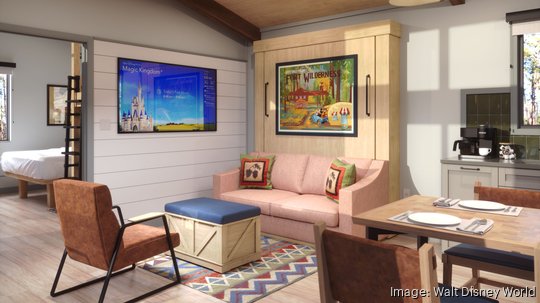
“We do thousands of renovation, maintenance and upkeep projects per year, plus small projects like a new restaurant or merchandise shop. But this is kind of quasi renovation of an existing asset and a new resort all at the same time,” he said.
After toying with ideas for a couple of years and not landing on a cabin design that quite worked, staffers from Disney asked some of the company’s regular contractors to participate in a design competition and paid each $5,000 to engage, said CEO Jeff Friedrich of Friedrich Watkins Company, an Orlando-based general contractor.
The scope included a standout mandate: The design had to translate easily into manufacture such that 365 cabins could be produced in 365 days.
“We thought, how are we going to get that many done in that period of time?” said Friedrich. “That’s where we got the idea of trying to modularize everything, trying to make it so we can bring a unit out on a trailer and put it all together in a couple of days."
For this project — and others before — Friedrich Watkins Co. and JCQ Services joined forces to pursue the contract. Their operating name is J&J Venture Group, and between them, 500 people are employed on the project. They brought in Windermere architecture firm Studio1+ because they thought they'd get a fresh approach to the design, said Friedrich.
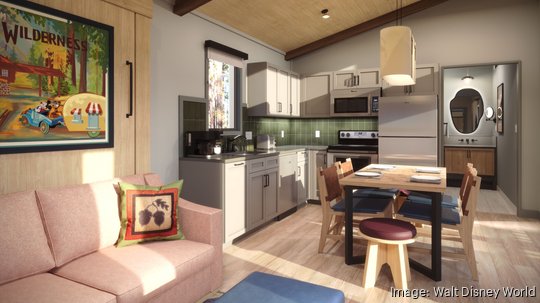
Having won the contract, J&J Venture Group is now deep into production. Orlando Business Journal toured a 100,000-square-foot warehouse where off-site prefabrication was well underway.
Watzel said doing so much of the work off site has reduced disruption at the resort, which has stayed open during the transition.
In the warehouse, all the elements that go into completing a cabin are organized as if inside a giant California Closet.
Some of those pieces are made with a Framecad machine that can read design documents created with Walt Disney Imagineers. In goes rolled steel sheeting and out comes customized metal studs.
"It drills and dimples them. It punches all the holes for all the mechanical electrical stuff to go through the walls, and it does it with less than 1% waste,” said CEO Juan Quiroga of JCQ Services.
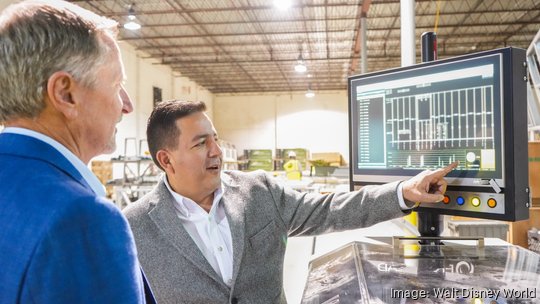
The leftovers are deposited into a bucket on the manufacturing line and recycled for other uses.
Framecad produces the structural elements for a cabin in two hours, and once made, they are assembled to the degree that they can be transported while vertically stacked on an A-frame truck, looking much like a glass delivery in progress.
"When everybody heard we were pre-building cabins, they thought we were fully building them and dragging them out to the site,” said Watzel. “But it's more like a kit of parts. You won’t see a cabin coming down the highway.”
Once on site, assembly takes the remainder of a day. That includes all the finishes like electrical, plumbing, sprinklers and mini-split air conditioners. Watzel said every choice along the way yields an efficient product. Disney likes to get to 40% below the American Society of Heating, Refrigerating & Air Conditioning Engineers national standards for efficiency on all of its new projects, he said.
“I think this one will end up penciling in the high 60%.”
Sign up here for the Business Journal's free morning and afternoon daily newsletters. Follow us on LinkedIn, Facebook, X and Instagram.