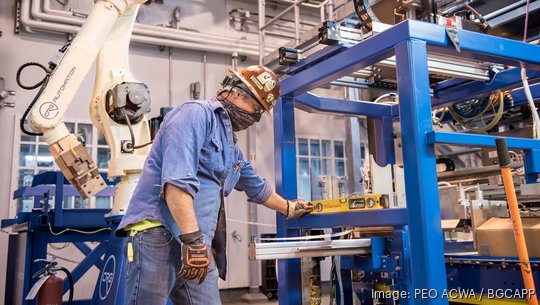
When talking about her employer, CRG Automation, Rebekah Fischer tried her best to sum up its mission: “Our favorite thing in the world is to solve problems that leave most people scratching their heads.”
The last problem the Louisville-based company helped solve involved the health and safety of the world, for it was CRG Automation that played a role in helping properly destroy the last two stockpiles of chemical weapons in the U.S.
The final warhead was drained of sarin nerve gas on July 7 at the Blue Grass Chemical Agent-Destruction Pilot Plant in Richmond, Kentucky. When that warhead was sent off to an on-site static detonation chamber, it was carried in a canister that was designed and manufactured by CRG Automation. The canister was composed of a steel tube and and a custom aluminum cap.
The rocket containerization system the company used was a combination of traditional industrial robots as well as state-of-the-art autonomous robots.
In total, there were 523.4 U.S. tons of chemical agents destroyed at the Richmond plant. The technology that CRG developed also was used in destroying 2,613.2 U.S. tons of chemical agents at the Pueblo Chemical Agent-Destruction Pilot Plant.
“We were a small part. We [provided] the tools to help them get across the finish line, but it’s pretty cool to be a part of … You can actually process a chemical warhead without anyone being in the room,” said Fischer, the company’s director of business development.
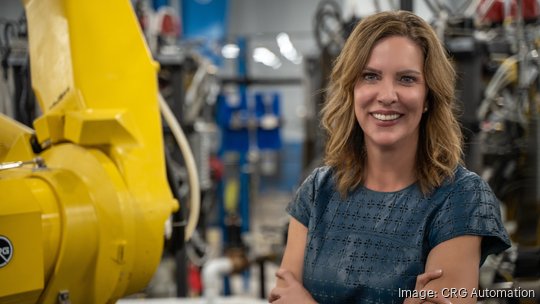
Fischer began working for CRG in July 2022. She is a younger sibling of the company's president and CEO, James DeSmet, who bought the company in 2020 when the name changed from CRG Technologies (founded in 2000) to CRG Automation. Before the acquisition of CRG, DeSmet worked as the global vice president of engineering and operations.
“This is one of the best projects I have ever been involved with. Great team, excellent collaboration, difficult problems to solve, mission critical to our country, tight (almost unreasonable) timelines — and oh yeah, there was Covid and a global supply chain disruption! Just another day,” DeSmet said in a statement provided by Fischer.
Conversations were just being started about the chemical weapon destruction initiative, Fischer said, when DeSmet had started the process of acquiring the company. The company was sought out by Amentum, a government and commercial services contractor, also known in the industry as a “prime.”
“We were actually brought in on a packaging problem,” Fischer said.
Along the way, the CRG team had to overcome a series of obstacles — among them the fact that when the warheads were constructed they were done with the intention of never having to be unassembled. The team ended up creating the Vertical Rocket Cutting Machine (VRCM), which functions as an industrial pipe cleaner that can separate the warhead from the rocket motor with incredible precision, Fischer said.
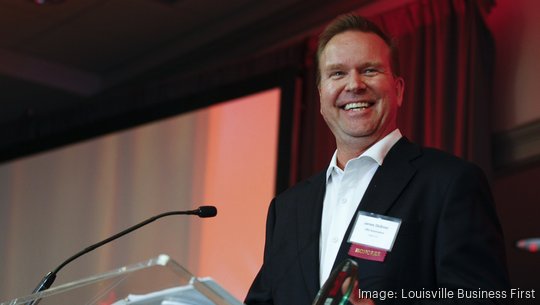
Furthermore, the team also had to ensure that there were no “leakers,” given that some of the chemical weapons had been stored for 60 years. To solve that issue, an examination system was created to catch any “leakers” before they entered the processing line.
The initiative is a part of the U.S. Department of Defense’s Program Executive Office’s Assembled Chemical Weapons Alternatives program. Per a press release, PEO ACWA, as it is known, destroyed 101,000 rockets and projectiles through five separate munition destruction campaigns, the last of which ended in Richmond on July 7.
PEO ACWA was tasked with the deadline of completing the destruction of all chemical weapons in U.S. control by Sept. 30, 2023, in keeping with the commitment date set by the Chemical Weapons Convention that went into effect in 1997.
What’s next
CRG Automation was No. 6 on Louisville Business First's Fast 50 list for 2022 after recording a revenue jump of 410% with more than $30 million in revenue in 2021, compared to $5.9 million in 2019. The company was also a recipient in our 2021 edition of Fast 50 as well.
In addition, as we reported, it was also named as one of the world’s 10 most innovative companies in 2022 by Fast Company. It was also named on our Best Places to Work in Greater Louisville list in 2022.
The company is located in a 40,000-square-foot facility located at 1700 Watterson Trail in Jeffersontown. There are plans, though, being drawn up for a 20,000-square-foot expansion, Fischer said, with the hope to break ground in early 2024.
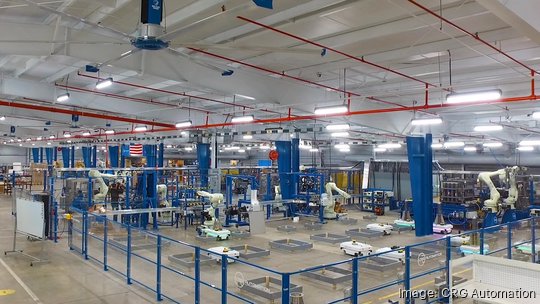
It is inside the large building where CRG builds exact replicas of their customers’ facilities and the equipment that will be implemented. Once the customer approves the process and equipment through a factory acceptance test, the site is disassembled, shipped and then reassembled on-site. In the case of the Richmond facility, the first equipment was being assembled in late 2020, Fischer said.
Its main clientele includes a list of large corporations who run a multitude of automated processes in their factories such as Coca-Cola, Reynolds and Kraft.
CRG has a headcount of 34 employees, 33 of which work out of the Jeffersontown facility. Fischer added, though, that they “are always looking for incredibly talented people to join our group.”
Going forward, CRG Automation hopes to continue to work in a similar capacity with the government, but with creation of 155 mm-caliber missiles, which have had documented shortages and have played a key role in helping Ukraine defend itself in the ongoing Russo-Ukrainian War.
“You hear about it every day … about how many [missiles] we’ve sent to Ukraine, and how our stockpiles are low. We have some pretty incredible technology that could really help that industry as well,” Fischer said. “We are raising our hand and looking to help [industrial bases] to automate processes to increase their production.”