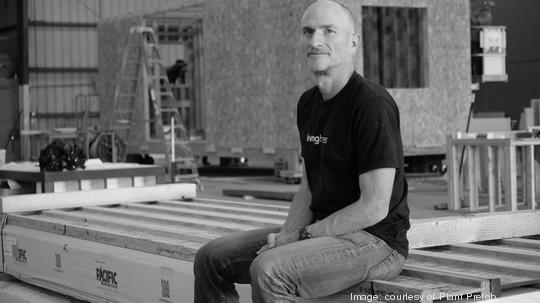
Steve Glenn's childhood dream was to become an architect.
While a traditional building design career didn't pan out, instead embarking on a career in tech, he nevertheless held onto his passion to facilitate "great architecture." In 2006, he founded LivingHomes to design and develop prefab homes.
He experienced challenges finding factories that could consistently meet his studio's expectations for quality and sustainability, he said. So he created a system to provide a "more efficient, more flexible, higher-quality" method that could work for any architectural style, in any location, especially in dense urban environments.
Ultimately, he created Plant Prefab and launched the company in 2016.
The company manufactures 3D-modeled, factory-fabricated homes, with the goal of bringing them to market faster and with higher quality than traditional methods.
"Our processes and controlled factory setting deliver a level of quality more akin to manufacturing than construction," Glenn said.
The company is headquartered east of L.A. county in Rialto, with a design studio and show home in Santa Monica. It has factories in Rialto and Ontario and is finishing up work on a regional production factory in Tejon Ranch.
Market Conditions
With a national housing shortage estimated at 4 million homes, the most in-demand urban infill, a term for rededication of open land in an urban environment to new construction, and resort markets can be challenging for builders. That can be due to diverse local zoning and code requirements, skilled labor shortages, high labor costs and short building seasons in some areas.
Plant Prefab's pipeline reflects the demand for more homes. As of August, contractual backlog totaled more than $85 million, representing year-over-year growth of 58%, Glenn said. Contracts include workforce, affordable and market-rate housing.
Once at scale, its factory is expected to produce more than 800 housing units per year, he said.
Funding
Plant Prefab recently closed a $42 million Series C round, which included equity and debt financing.
The round, which included $30 million in equity, was led by Gerdau Next Ventures, the VC arm of Brazilian steel producer Gerdau. The rest was debt and equipment financing from Western Technology Investments and ATEL Capital Group.
The funds will be used to complete the automated factory in Tejon Ranch in Kern County, southeast of Bakersfield. This factory will serve the entire western part of the U.S. beyond California and Colorado, its current coverage area.
How it works
Plant Prefab’s patented system is a hybrid consisting of panels and modules.
The company's engineers create a detailed virtual model — a complete digital twin that includes every piece of material needed to build a specific home — so they can fully coordinate all the mechanical, electrical and plumbing work.
This enables them to find and fix any issues before a single board is cut, "shaving significant time off the construction schedule and preventing costly mistakes and rework," Glenn said.
The company also facilitates parallel construction. It works on manufacturing everything above the foundation, while the site general contractor prepares the lot and foundation. Once all the components are ready, a house can be assembled in just a few days, he said.
Competition
Glenn said Plant Prefab only competes with site-built construction, not other prefabricators like Boxabl. For example, Plant Prefab's panels and modules do not come on hinges to be folded out, Glenn said.
What differentiates Plant Prefab, Glenn said, is its flexible system that enables the company to fabricate almost any housing type — such as single-family homes, duplexes and apartment buildings — in any style of architecture.
"We can do steel or wood framing," Glenn said. "We can deliver just structural panels or fully volumetric modules that ship complete with all finishes, fixtures and appliances in place. We don't offer a set product or focus on a set segment of the housing market."
Recent home installation
Plant Prefab recently manufactured a four-unit, 6,000-square-foot multifamily development for a project in West Hollywood. The property is owned by Metros Capital and is part of a project to increase housing density on urban infill lots.