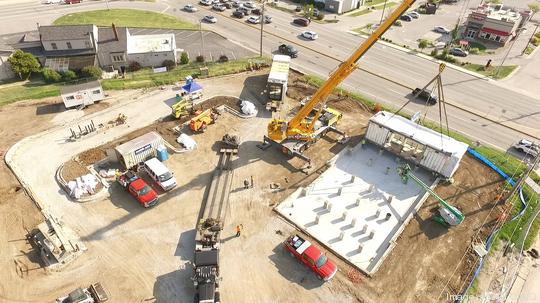
When local real estate firm CBRE Group Inc. approached Hoefer Welker about a prototype design study of buildings for its client, JPMorgan Chase Bank, Chris Armer said the architecture company was eager to get involved.
The new standalone branch, at 815 SW Highway 7 in Blue Springs, was completely constructed in a factory in Pennsylvania then shipped out to the site in pieces to be reassembled. The 3,300 square feet building was erected on site in just a few days.
Hoefer Welker was the project’s architect, with MODLOGIQ Inc. taking on the general contractor role.
Armer, a vice president at Hoefer Welker, said it was tasked to come up with ways to make the bank buildings more efficient, cost-effective, easier to build and bring them faster to market. JP Morgan was interested in prefabrication, so MODLOGIQ, a commercial modular manufacturing company based in Pennsylvania, came on board.
“They decided to do a test case out in Blue Springs to see if this would work and if this was a good idea,” Armer told the Kansas City Business Journal. “I think it is. Along the way, we discovered things that could be ironed out, but the whole thing was about how we get this quick to the market.”
Chase, Armer said, had full prototype drawings and knew exactly what it wanted and where, including finishes, where the tellers are located, where ATMs would go, and how big to make the lobby.
“One of the puzzles all along was how to make the prototype work in a modular way,” Armer said. “But it seemed to work out pretty well.”
Hoefer Welker’s team had to determine the best places to chop the building into pieces to fit in the module. The modules needed to be small enough to transport on highway and were limited to around 15 feet in width. The widest module, the building’s lobby, needed to be as wide as possible.
“It was an interesting exercise,” Armer said. “All these modules are essentially individually framed to support themselves and they have to be supported in transport, and they have to be supported by being lifted in the air. So, they’re very stout and have a lot of structure in them. Then you take those pieces and mush them together.”
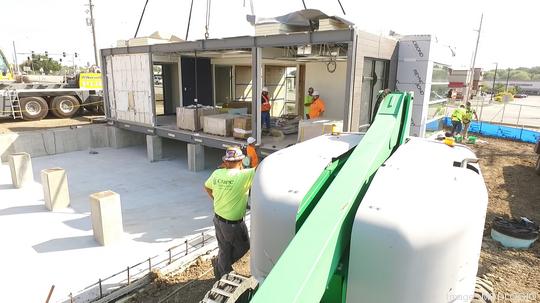
Although the project began in December 2020, supply chain delays pushed back its completion. Armer said he envisions similar projects being completed in about six months. This method of prefabrication cuts six months to a year from a traditional build project.
“I’m fascinated by it, and I’m trying to get as many people as we can out to see this process,” Armer said. “In some of our other markets, it almost seems like a no-brainer.”
When the hospitality industry sees an uptick again, Armer believes this module is perfect for building hotels.
“You can do the whole thing, from room-to-room, put it on a truck and go,” Armer said. “Then you can stack them up and put a hotel in in just a week.”
He also said this build process could be an advantage to health care clients, like hospitals looking to add on without affecting operation. With the prefabricated modules, the hospital stays up and running and the installation can be finished in about a week.
Hoefer Welker also has looked at prefabrication for multifamily projects, which Armer said is a booming business. Although the approach may not save money, it saves time.
“You can imagine how that calendar looks with four months of site work and a year of construction,” Armer said. “We’re doing the site work at the same time the building is being built. So, once it’s ready, they’ll spend a couple of days zipping it up, and then they’ll walk away.”
The teams will bring all their thoughts together in the coming weeks and figure out how they can improve on what they did, and possibly build similar buildings in the future.
“I think they see that this has been an absolutely tremendous opportunity for them to put up banks really quickly,” Armer said.