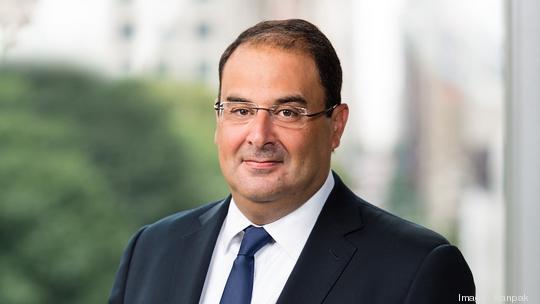
Omar Asali has strong feelings about manufacturing.
The chairman and CEO of Ranpak Holdings Corp. is an immigrant from Jordan who fell in love with American manufacturing as an investor.
That love deepened when Asali took over as leader of Ranpak after his family office invested in and then took public the Concord Township, Ohio, company, which makes eco-friendly packaging technologies and materials.
Ranpak makes the paper dispensing machines that fold, cut, bunch, crimp and stitch kraft paper to use as packing for everything from meal kits to aftermarket automotive parts.
Asali talked with me about how Ranpak is investing in automation and other technologies that are boosting the company's productivity but also creating a new generation of jobs at his company. This interview has been edited for clarity and brevity.
What do you think about the United States moving to a service economy from a manufacturing economy since World War II?
I think that was a mistake. Manufacturing is how you create wealth. I think there is a lot of manufacturing that can be done here. And I think we should offer a great career path for people who decide they want to play a role in an industrial or manufacturing company. I'm quite proud that we are part of the manufacturing industrial wave.
What does automation have to do with Ranpak's manufacturing operations?
Ranpak makes the equipment that configures paper and other materials into packaging or customizes the shipping boxes for more efficiencies. We're involved in robotic arms to place items in the boxes. We are a company that has terrific engineering, and we understand paper extremely well. We are deep experts in the interaction between equipment and paper to come up with these solutions.
We own a small automation business near Heerlen in Kerkrade, Netherlands, which we have been investing behind and expanding and making more of a global offering. And they've hired a lot of engineers computer scientists, technical people to expand that business and to accelerate Ranpak's global leadership in packaging automation.
Ranpak also recently created R Squared Robotics, a division that uses 3D computer vision and artificial intelligence to improve end-of-the-line packaging and logistics.
Your company recently announced an investment in Pickle Robot Co., which makes robots for automated sorting, loading and unloading of packaged goods within supply chain systems. What does this investment mean for Ranpak?
Pickle Robot has developed a low-cost, collaborative package-handling robot that automates several key tasks along the e-commerce supply chain, which is a very important market segment for us. The investment in Pickle Robot solidifies our focus on automation and unlocks new opportunities to deliver efficiencies, cost-savings and value to our global customers.
Ranpak Automation, along with Pickle and R Squared Robotics, will design and build automated and integrated systems for high-volume operations to improve their speed and efficiency. By harnessing the power of artificial intelligence and robotics, Ranpak is driving transformation of the fulfillment and packaging industry.
Doesn't automation replace workers in your factories?
One of the big misnomers about automation is that it kills jobs. Really, that's not it. It brings certain efficiencies and moves jobs around. Maybe the skill set needs to evolve, but I think automation creates a lot of job opportunities.
People used to talk about e-commerce killing retail jobs, but e-commerce created a lot of warehouse jobs. And automation is going to have a similar impact where jobs will be shifted around.
When we took the company public, I gave every employee including temporary workers equity in the company. It meant a lot to people, and we continue to invest in our culture. And a big part of it is you know, continuing to provide the right financial incentives to people who work in our factories.
But I'll be honest with you, it's a bit more than just financial incentives and money. You know, giving them the respect and the recognition that they really are doing a lot of difficult work at a very difficult moment in history. I think that's important to them as much as the financial incentives that we provided. Without them, we couldn't succeed.