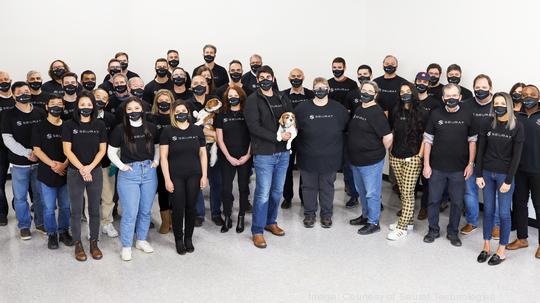
Additive manufacturing and 3-D printing are becoming mainstream. More and more people are dabbling in them, from teens spending a couple of hundred dollars for a personal 3-D printer to large aerospace companies setting up their own additive-manufacturing programs. Seurat Technologies is betting that its technology and business model can stand out and stand the test of time.
The Wilmington-based company is combining its technology, which Seurat says lets it scale printing rates without losing resolution, and its business model, which involves locating its additive-manufacturing facilities near its customers. The goal is to reduce costs for customers and improve Seurat’s own margins.
CEO and co-founder James DeMuth said the company’s approach lends itself to scaling quickly. They aim to have more than 1,000 employees by 2030 working at its sites to produce parts for the consumer electronics, automotive, energy, aerospace and medical industries. Seurat plans to have a little over 100 employees at the end of this year.
Seurat was founded in 2015 after DeMuth spent time working at Lawrence Livermore Labs in California. His team was working on a nuclear fusion energy project with an extremely powerful laser. To withstand that environment, DeMuth said they realized they needed a fusion chamber built from special alloys that could not be welded but could be 3-D printed. The only problem, he said, was 3-D metal printers would have taken decades to make a single chamber. This began DeMuth’s search for a new approach to additive manufacturing.
DeMuth recently spoke with BostInno about the company’s launch and move to Massachusetts, its unique business model, the future of additive manufacturing and more.
When you founded Seurat in 2015, you were still based in California. Why make the move to Greater Boston?
Boston has been a 3-D printing hub or mecca for the world for a long time, since like the 1990s. It started with Z Corp., and MIT and there’s just been new additive technologies congregating in the Boston area, leveraging expertise in automation, robotics, high-temperature furnaces, telecom. All of those different industries have sort of made it a good hotbed.
The actual density of additive-manufacturing companies in the Boston area is greater than anywhere else in the world. So it truly is really a hub for 3-D printing.
You’ve said that current 3-D printing with lasers is like “writing a letter with a pen,” but your approach is like “the printing press.” What does that mean?
We essentially take next-gen laser technology that’s got incredible scalability and we build machines that do additive manufacturing with it. We then operate those machines — we don’t sell them — we operate them to print parts for customers. We deploy part printing factories at or near customer sites, large OEM sites, to print parts on demand where they’re needed, when they’re needed.
Why did you go with this business model for Seurat?
We get fantastic economics as we scale our architectures to subsequent machine generations, which allows us to pass along that cost savings to customers and improve our cost margins along the way. We can get to per part price points that are fantastic. I mean we’re talking about our goal by 2030 to have a machine capable of printing parts for less than $25 a kilo. Just to put that in perspective, your silverware costs $35 a kilo to make.
As we go to these bigger machines, we can get to these fantastic price points. It doesn’t come with shipping a lot of small machines; it comes with deploying big machines.
And when you do part production, you sign customers up for long-term production agreements that span multiple years. And now you’ve got security and visibility into what your revenues are going to be multiple quarters out. And that’s critical if you’re ever looking to go public, as an example.
Where are you setting up these machines?
We’re in the process of deploying our pilot plant. So our pilot plant is small. It’s going to have three machines. We’re just about to sign a lease on a site that’s going to become our first production plant. This will house around 30 machines. That will also be in Wilmington, Massachusetts, or close by.
From there, the next deployment will likely be in the U.S. Perhaps Detroit. We will see. Somewhere that’s a manufacturing hub.
Where do you see additive manufacturing in the next decade or so?
I think our goal by the end of 2030…we’re talking tens of thousands of metric tons of metal are being printed each year on additive machines. We’re talking about penetration into just machining but also casting and low volume forging industries. We’re talking about parts being mass produced via this technology that are meeting all customer standards and requirements for quality, yet also outstanding price and performance values.
What I think I’m most excited about is that if you can now say you’re making additive manufacturing parts at conventional manufacturing prices, now we’re going to see a paradigm shift where engineers need to now think differently. You don’t design parts for the manufacturing process. Design the part for how it really needs to perform. Let performance-based design dictate what you do, as opposed to manufacturing method-based design.
Sign up for The Beat, BostInno’s free daily innovation newsletter from BostInno reporter Hannah Green. See past examples here.