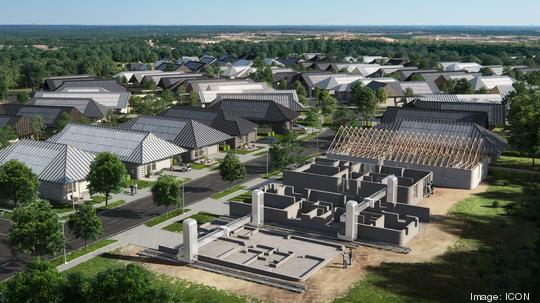
Icon Technology Inc. is getting into the volume homebuilding game. The Austin-based company announced this week that it has joined forces with Lennar Corp. to develop a 3D-printed, 100-home community in a yet-to-be-announced location somewhere in the area.
According to the announcement, it will be the largest 3D-printed community in the world to date. It’s set to break ground in early 2022. International architecture firm Bjarke Ingels Group, or BIG, will help design the community.
Icon is a unique company — one at the cutting edge of homebuilding technology but with eyes on other frontiers, too. The company received a U.S. Air Force contract in 2020 to develop technology for building structures on the moon.
Since its inception in 2017, the company has been busy. It has also built 3D-printed homes for impoverished families in Mexico with nonprofit partner New Story. Icon's first for-sale 3D-printed homes hit the market in East Austin in March.
This deal with Lennar (NYSE: LEN) is pivotal because it will offer the first demonstration of Icon's technology in a large-scale community in the United States, in partnership with a traditional volume builder. It should demonstrate whether 3D homebuilding can significantly impact communities like Austin with major housing shortages.
The company’s proprietary “Vulcan” construction machine can produce houses up to 3,000 square feet. According to the company, the materials are believed to be longer-lasting and more weather-resistant than traditional homebuilding materials.
“The 3D-printed architecture and the photovoltaic roofs are innovations that are significant steps towards reducing waste in the construction process, as well as towards making our homes more resilient, sustainable, and energy self-sufficient,” Martin Voelkle, partner with BIG, said in a statement.
Slideshow: Photos from earlier this year when Icon's first for-sale 3D-printed homes hit the market in East Austin.
PHOTOS & RENDERINGS: 3D-printed homes in Austin, Texas
Miami-based Lennar is one of the largest homebuilders in the U.S. and in the Austin area. According to Austin Business Journal list research, Lennar was the second most productive volume homebuilder in Central Texas last year with $548.39 million in home sales, behind only D.R. Horton.
Lennar’s local portfolio spans a wide range of prices, from the low $200,000s to upwards of $1 million, in places from Hutto to Marble Falls.
Lennar was among the investors in Icon's recent $207 million series B funding round. The round, one of the biggest fundings for an Austin-based company in 2021, was led by Silicon Valley-based venture capital firm Norwest Venture Partners.
A spokesperson from Lennar said Icon's technology is the most “advanced and proven” on the market.
The promise of a faster, more cost-effective homebuilding method is particularly welcome in Austin, where housing stock has dwindled to about one-sixth of a healthy level. According to the Austin Board of Realtors, there was only 1.1 month of housing inventory in the Austin metro area in September.
“Labor and material shortages are two of the biggest factors pushing the dream of home ownership out of reach for many American families,” Eric Feder — president of LEN X LLC, a technology-focused arm of Lennar — said in a statement.
Icon co-founder and CEO Jason Ballard said the housing crisis was the impetus behind his company's creation. He said the most powerful applications of 3D technologies are for products that are otherwise large, slow-to-make and customizable.
“Houses are probably the best application for the technology,” Ballard said.
Ballard said there are no real comparable homebuilding techniques to 3D printing. The process bypasses many of the biggest hurdles in the housing market right now, including material and labor shortages. He also pointed to another powerful advantage of 3D printing for homes: speed. The company has previously stated it can print a home in about 48 hours, but it's unclear whether that estimate will differ for the larger-scale production.
“Ultimately, to win the war — not just the battle — for decently priced houses, you have to outrun the supply and demand issues,” Ballard said.
For this new larger-scale community, Icon invested in a new factory in South Austin, a move made possible by its series B funding round. Ballard said while this move expands the application of its tech to hundreds of homes, leaders hope to start producing thousands of homes “as fast as possible.” Part of the reason for Icon's expansion is to accommodate growing demand, he said.
“We need to radically increase the supply of this technology, so we can start saying yes to more of these opportunities,” the chief executive said.
